In the previous post, I wrote about using my CNC mill to depanelize PCBs. One issue I had was that the boards were not cleanly separated from the panel since they moved away as soon as the mill broke through the tab connecting them to the panel, leaving a pointy feature.
I tried to improve this by using double sided tape to keep the boards in place:
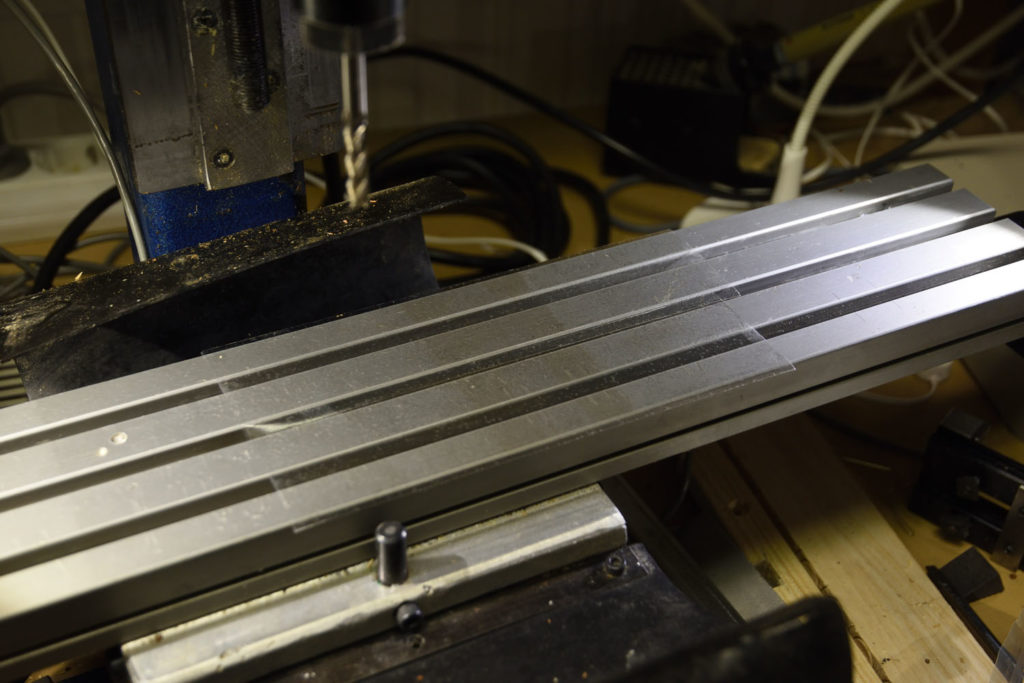
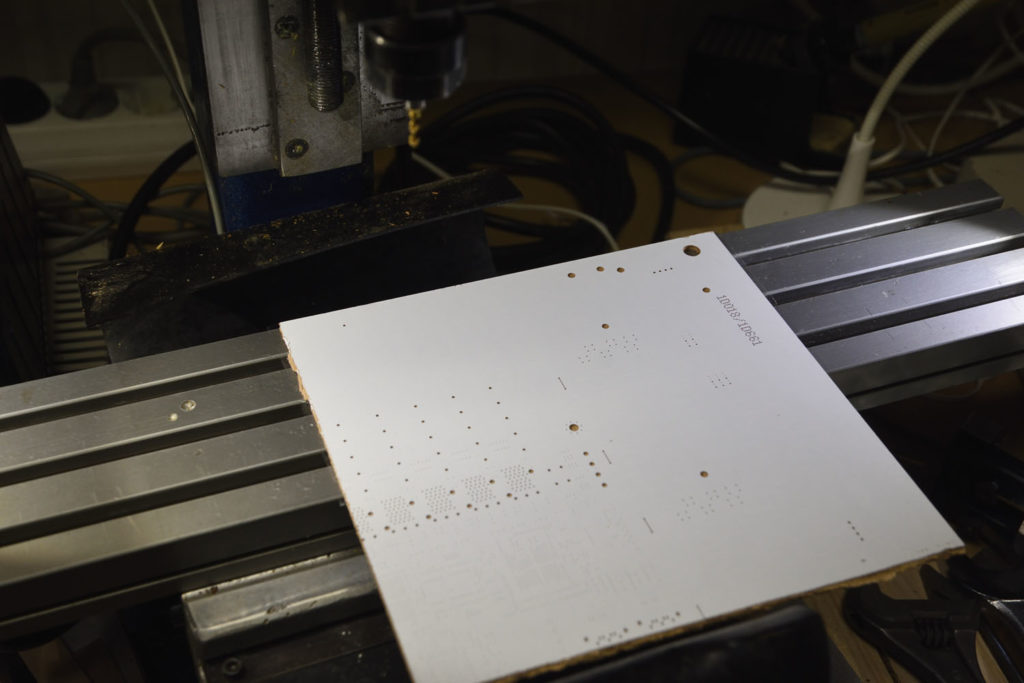
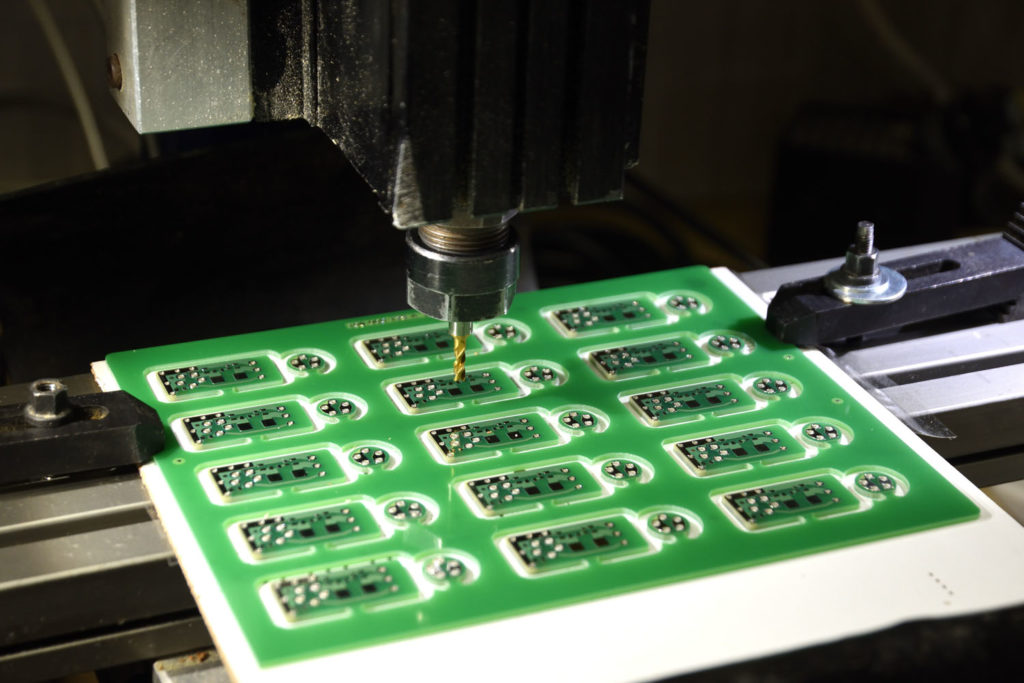
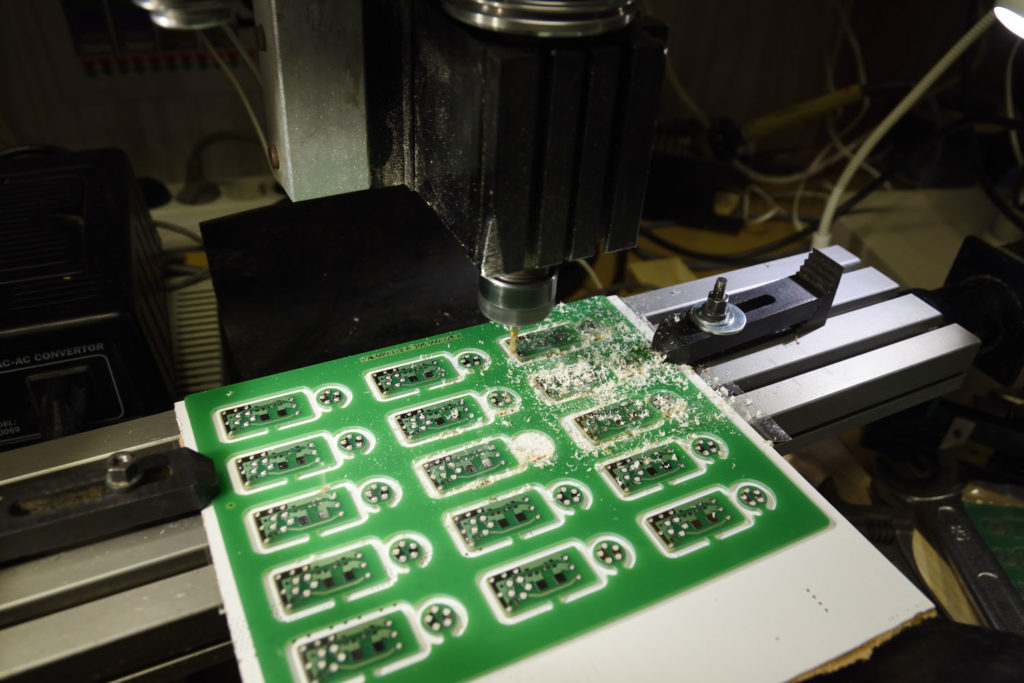
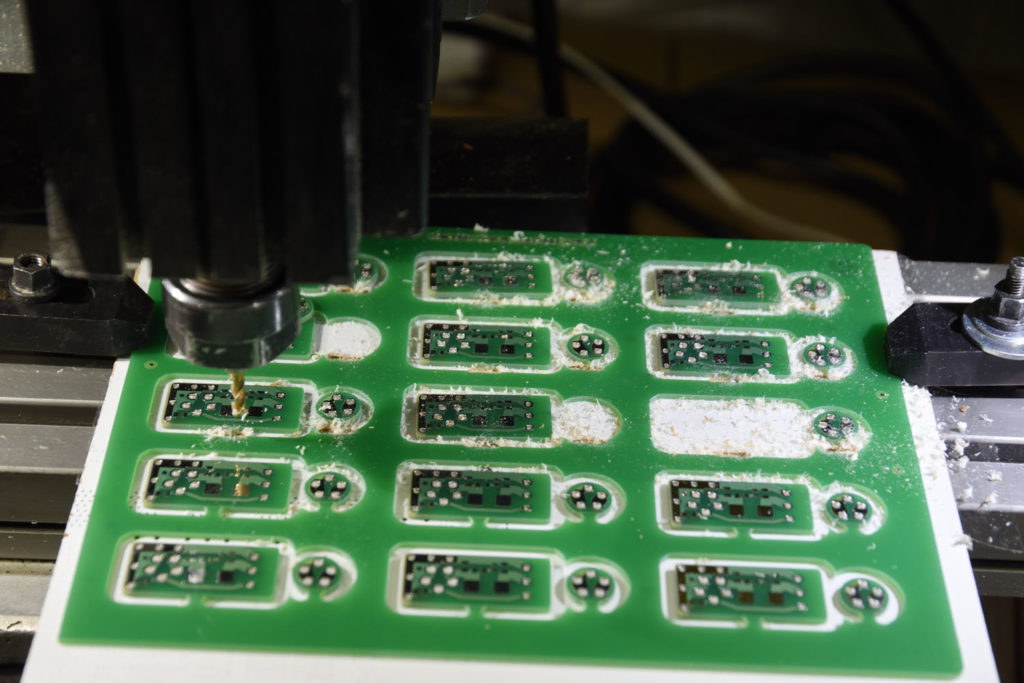
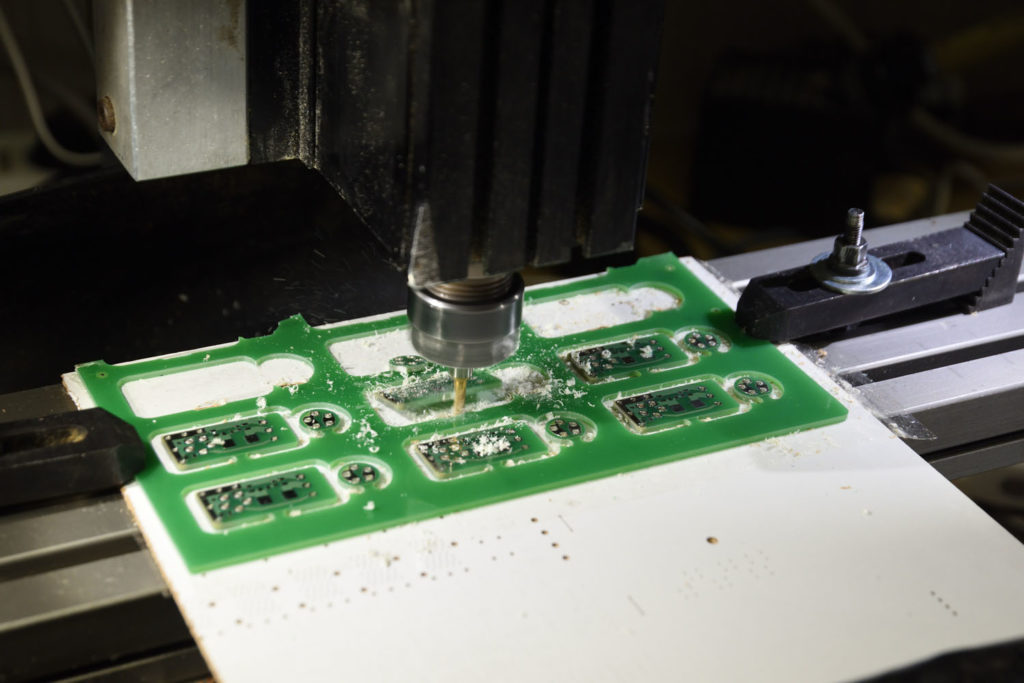
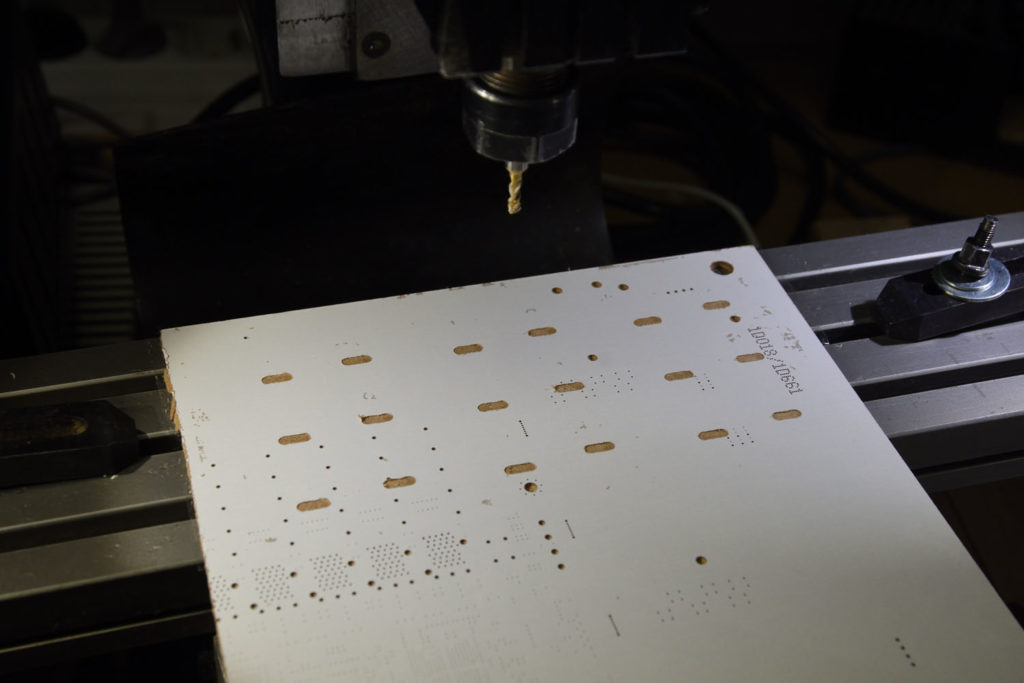
In summary, using double sided tape to aid in the workholding is a promising idea. With the small board in this panel it was however only semi-successful since the adhesive has very little area to attach to and the PCB surface is a bit uneven due to the trace pattern. On larger boards it will probably work better.